We use cookies to enhance your experience. By continuing to browse this site you agree to our use of cookies. More info.
In aerospace manufacturing, the use of high-temperature alloys has enabled the development of more reliable and efficient aircraft that ensure the safety of both crew and passengers. High-temperature alloys have also facilitated the development of fuel-efficient engines that reduced the environmental impact of air travel. This article discusses different high-temperature alloys used in aerospace manufacturing. Rhenium Element

Image Credit: AMatveev/Shutetrstock.com
High-temperature alloys are a critical component used in aerospace manufacturing. These alloys are designed to withstand extreme conditions encountered by an aircraft during its flight, including high stress, temperature, and pressure. Titanium alloys and nickel alloys are the most extensively used high-temperature alloys for aerospace applications.
Nickel alloy 625 is one of the commonly used high-temperature alloys for different aerospace applications. This nickel-chromium alloy possesses exceptional corrosion resistance and a high level of strength and can be fabricated easily.
Nickel alloy 718, nickel alloy A-286, and nickel alloy 625 can be utilized in jet engine hot sections as they are highly resistant to both corrosion and oxidation. Nickel alloy A-286 and nickel alloy 718 are also resistant to high-temperature fatigue, which occurs due to repeated cooling and heating cycles experienced during flight.
Titanium alloys are another commonly used high-temperature alloy used in aircraft engine component and structure production. Titanium Grade 5, containing 4% vanadium and 6% aluminum (Ti 6Al-4V), is used extensively in aerospace applications.
Titanium is lightweight and possesses exceptional resistance to corrosion and high temperatures, which makes it suitable for aerospace applications, specifically for the hot sections of jet engines.
GRCop-84 is a copper-based high-temperature alloy/copper-chromium-niobium alloy that possesses improved oxidation resistance, long low-cycle fatigue, good creep resistance, and excellent strength at elevated temperatures.
Moreover, the thermal expansion of GRCop-84 is significantly lower compared to copper and low-alloy copper-based alloys. The alloy can be produced in different shapes, such as sheet, plate, bar, and tubing, using standard production techniques, such as bending and stamping.
GRCop-84 alloys can be joined using electron beam welding, diffusion bonding, inertia welding, and friction stir welding. The alloy offers potential for high-heat-flux applications up to 700 oC while it is specifically designed for main combustion chamber (MCC) liners of rocket engines.
In a study published in the journal Scientific Reports, researchers developed a new MoSiBTiC alloy that surpassed the capabilities of nickel high-temperature alloys for aerospace applications.
The MoSiBTiC alloy possesses a high-temperature strength under constant forces within the 1400 oC -1600 oC temperature range, which makes it suitable for aircraft jet engines. The alloy is significantly stronger compared to nickel-based single-crystal superalloys that are commonly utilized in hot sections of jet engines.
Moreover, the MoSiBTiC alloy can withstand disruptive forces without deforming under ultra-high temperatures, as it has exceptional creep strength with reasonable creep parameters.
The use of alloys containing several critical elements is increasingly becoming necessary in several aerospace applications. However, the rising cost of critical raw materials due to their growing utilization in multiple applications and high-tech products has led to high supply risk, which necessitated the identification of viable solutions to reduce critical raw material usage.
A suitable surface treatment or a coating on the alloy can be a viable solution to reduce the critical raw material usage and preserve a high-temperature alloy by prolonging its operational lifetime and ensuring its safe operation in harsh conditions, such as extreme low/high temperatures, high mechanical stresses and pressures, corrosion/radiation, and high thermal shocks.
Thus, coatings can be applied to nickel and titanium-based high-temperature alloys used in aircraft engines to conserve raw materials. These coatings act as diffusion barriers that slow down the reaction between the substrate alloy and the aggressive environment.
For instance, thermal barrier coatings can be used for nickel-based superalloys in aerospace components of the hot sections of the engine to enable those components to effectively withstand severe working conditions.
The engine operating temperature can be increased beyond the melting point of the high-temperature alloys to achieve a better fuel efficiency conversion using thermal barrier coatings and cooling systems.
Typically, a 200 °C rise in service temperature can lead to a 5–6% increase in turbine efficiency, which can result in a significant reduction in nitrogen oxide and carbon dioxide emissions in the atmosphere.
The thermal barrier coating system used to protect the nickel superalloys consists of two key layers, including an oxidation-resistant bond coat such as diffusion aluminide or an overlay nickel/cobalt-chromium-aluminum-yttrium (MCrAlY) bond coating and a ceramic top coat.
Different coating methods/surface treatments can be used to protect titanium-aluminum-based high-temperature alloys from oxidation in aerospace applications. For instance, surface treatments, such as plasma electrolytic oxidation (PEO), laser shock peening (LSP), spraying, ion implantation, plasma nitriding, and thermal oxidation, can improve the poor tribological properties of titanium alloys.
To summarize, high-temperature alloys for aerospace applications manufactured using critical raw materials are playing a crucial role by enabling aircraft components to endure severe conditions. Coating/surface treatments can be used to realize better performance from these alloys and conserve critical raw materials.
More from AZoM: The Role of Composites in Aerospace Engineering
Kamata, S. Y., Kanekon, D., Lu, Y., Sekido, N., Maruyama, K., Eggeler, G., Yoshimi, K. (2018). Ultrahigh-temperature tensile creep of TiC-reinforced Mo-Si-B-based alloy. Scientific Reports, 8(1), 1-14. https://doi.org/10.1038/s41598-018-28379-w
Grilli, M. L., Valerini, D., Slobozeanu, A. E., Postolnyi, B. O., Balos, S., Rizzo, A., Piticescu, R. R. (2021). Critical Raw Materials Saving by Protective Coatings under Extreme Conditions: A Review of Last Trends in Alloys and Coatings for Aerospace Engine Applications. Materials, 14(7), 1656. https://doi.org/10.3390/ma14071656
Ellis, David. (2005). GRCop-84: A High-Temperature Copper Alloy for High-Heat-Flux Applications. [Online] Available at https://ntrs.nasa.gov/api/citations/20050123582/downloads/20050123582.pdf (Accessed on 19 July 2023)
High Temperature Alloys in Aerospace [Online] Available at https://supraalloys.com/aerospace-high-temperature-alloys/ (Accessed on 19 July 2023)
Disclaimer: The views expressed here are those of the author expressed in their private capacity and do not necessarily represent the views of AZoM.com Limited T/A AZoNetwork the owner and operator of this website. This disclaimer forms part of the Terms and conditions of use of this website.
Samudrapom Dam is a freelance scientific and business writer based in Kolkata, India. He has been writing articles related to business and scientific topics for more than one and a half years. He has extensive experience in writing about advanced technologies, information technology, machinery, metals and metal products, clean technologies, finance and banking, automotive, household products, and the aerospace industry. He is passionate about the latest developments in advanced technologies, the ways these developments can be implemented in a real-world situation, and how these developments can positively impact common people.
Please use one of the following formats to cite this article in your essay, paper or report:
Dam, Samudrapom. (2023, August 01). The Best High-Temperature Alloys for Aerospace Applications. AZoM. Retrieved on November 08, 2023 from https://www.azom.com/article.aspx?ArticleID=22897.
Dam, Samudrapom. "The Best High-Temperature Alloys for Aerospace Applications". AZoM. 08 November 2023. <https://www.azom.com/article.aspx?ArticleID=22897>.
Dam, Samudrapom. "The Best High-Temperature Alloys for Aerospace Applications". AZoM. https://www.azom.com/article.aspx?ArticleID=22897. (accessed November 08, 2023).
Dam, Samudrapom. 2023. The Best High-Temperature Alloys for Aerospace Applications. AZoM, viewed 08 November 2023, https://www.azom.com/article.aspx?ArticleID=22897.
Do you have a review, update or anything you would like to add to this article?
In this interview, Dr. Stuart Wright, a Senior Scientist at Gatan/EDAX, talks to AZoMaterials about the versatile applications of Electron Backscatter Diffraction (EBSD) in materials science and metallurgy.
In this interview, AZoM speaks with Ger Loop, Product Manager at Avantes, about Avantes' impressive 30 years of spectroscopy experience, their mission, and the future of their product lines.
In this interview, AZoM speaks to LECO's Andrew Storey about glow discharge spectrometry and the opportunities offered by LECO's GDS950.
The ClearView® high-performance scintillator camera elevates everyday transmission electron microscopy (TEM).
The XRF Scientific Orbis laboratory jaw crusher range features dual-action fine crushers, with jaw efficiency allowing samples to be reduced by up to 55 times their original size.
Discover Bruer’s Hysitron PI 89 SEM PicoIndenter—a state-of-the-art PicoIndenter for quantitative in-situ nanomechanics.
The global semiconductor market has entered an exciting period. Demand for chip technology is both driving the industry as well as hindering it, with current chip shortages predicted to last for some time. Current trends will likely shape the future of the industry, which is set to continue to show
The primary distinction between graphene-based batteries and solid-state batteries lies in the composition of either electrode. Although the cathode is commonly changed, carbon allotropes can also be employed in fabricating anodes.
In recent years, the IoT is rapidly being introduced into almost all sectors, but it has particular importance in the EV industry.
AZoM.com - An AZoNetwork Site
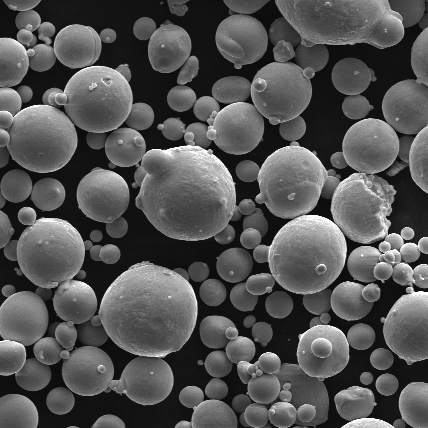
Plasma Thermal Spray Owned and operated by AZoNetwork, © 2000-2023