Bright. Bitter. Spicy. Citrusy. Layered. If there’s one thing we know, it’s that craft beer brewers aren’t in this line of work to blend in. Constantly in pursuit of new and better ways to capture, embody and deliver hop aroma and flavor, experimentation often tends to be the name of the game. And depending on the filtration process brewers choose to implement, the product produced could vary greatly not only in taste, but in color and turbidity as well — making filtration an essential consideration when creating and perfecting one-of-a-kind craft beers.
It comes down to the unique experience each beer delivers. Consumers expect craft brews to exude originality and maintain a unique character, which makes it even more important that the beer’s quality meets the highest standards. Precise quality characteristics can only be achieved by selecting the most appropriate methods and media for the filtration process, given the vital role it plays in the flavor, appearance and commercial success of the finished product. While the price of this individualism tends to come at higher investment and operating costs per gallon/hectoliter when compared to large-scale breweries, to set yourself apart from the crowd, it’s worth it. Industry Grade Diatomite

With such a strong focus on the craftsmanship involved in producing unique tastes, it seems almost contradictory that filtration plays such a decisive role in craft beer brewing. Especially when, in some cases, skipping filtration has even been used as a selling point. However, given completely unfiltered beer is seldom sold on the market, this usually only means that specific filtration steps have been skipped, not the process in its entirety. In fact, every craft beer undergoes filtration processes, with most differing greatly from those used for large-scale brewing.
This filtration is typically carried out in four steps.
In the first step of the filtration process — beer clarification — bag filters or centrifuges are used due to craft beer’s tendency toward high production volume and hop content. The aromatic profile of the beer can be enhanced by extra dry hopping, which involves adding hop content to the bag filter. If depth filter sheets/cartridges or stacked disc cartridges were used instead of bag filters or centrifuges, the direct exposure to such a large amount of hops would quickly result in them becoming blocked. Because of this, only coarse hop and yeast particles are removed during beer clarification.
The second clarification step can be performed in one or two steps, depending on the desired degree of filtration. More steps mean finer beer with a smoother mouth feel. The number of steps has a direct effect on the color of the beer as well, with clarifying filtration playing a decisive role in the appearance of the final product. How much foam the beer develops can also be influenced during clarification.
The third step — trap filtration and fine filtration — involves sheets, stacked disc cartridges or filter cartridges, sometimes with different filter media types. When should a brewer use each? For starters, if a brewer is only producing a small volume of up to 130 gallons (500 liters) of beer per week, it may be more appropriate to use stacked disc cartridges or depth filter cartridges, though ultimately this depends on the brewer’s philosophy and how they plan to market the craft beer in progress. This is due to sheet filters being more flexible than filter cartridges, whereas stacked disc cartridges and depth filter cartridges offer the advantage of an enclosed system. However, each of the three methods offers a very similar level of control over the characteristics of the craft beer, including its turbidity and appearance.
The fourth and final filtration step is performed before bottling to ensure optimal quality, especially regarding the beer’s appearance. Once again, the philosophy of the brewer plays a major role here. Deciding between 5- to 20-µm depth filter cartridges and stacked disc cartridges, which are typical of the craft beer brewing process, is important in this final step. While for home brewers the main focus may be on the turbidity of the beer, for larger-scale breweries ensuring that the beer contains as little yeast as possible is more important.
As they strive to set themselves apart, all brewers of craft beer agree on one thing hands down: Stabilization measures (like flash pasteurization HTST) are generally not required, as it would significantly change the aroma profile of the beer. Plus, these beers tend to be consumed not long after they are made, which often makes extending their shelf life unnecessary.
Knowing what results are desired once filtration is complete helps brewers select the appropriate filter media to use throughout the process. For example:
Aside from the actual brewing processes, filtration is also crucial for craft beer breweries in terms of the water used. Brewing craft beer usually requires using drinking water, which should be prefiltered. This helps ensure a consistent mineral content and pH value and prevents exposure to germs and other particulate matter. With retention rates of up to 0.2 µm, significantly higher than the filter media used at any of the beer filtration steps, filter cartridges are usually used for this purpose as well. That said, considerations for craft brewers vary by location. Here in the United States, for example, it’s important to be aware of water’s chlorine content, which has become increasingly too high. Activated carbon filters are used to prevent this.
In addition, because craft beer breweries do not require a “bright” product, precoating filtration using filter aids like diatomaceous earth and superfine membrane filtration using 0.45-µm membrane filter cartridges are not required during brewing. In fact, a small degree of turbidity is often very much desired. Which is why the filtration process is so important: It allows craft brewers to precisely control the turbidity of their beer. In the craft niche, brewers only want to filter out coarse yeasts and particles so that a certain level of turbidity is maintained. Thus, the filtration process is not aiming for brightness. It’s aiming for uniqueness, both in look and taste. Fresh. Earthy. Caramelly. Yeasty. Charismatic. Out of the box. Or, rather, the bottle.
Hans Peter Discher is a product manager with Eaton Technologies GmbH, Germany. Discher attended the University of Applied Sciences in Geisenheim, where he studied winemaking and beverages technologies to earn his Bachelor of Science degree. Following university, he joined Eaton’s Filtration Life Science sector in 2012, where he focuses on beer, spirits, wine, nonalcoholic beverage and food filtration processes.
You must be logged in to post a comment.
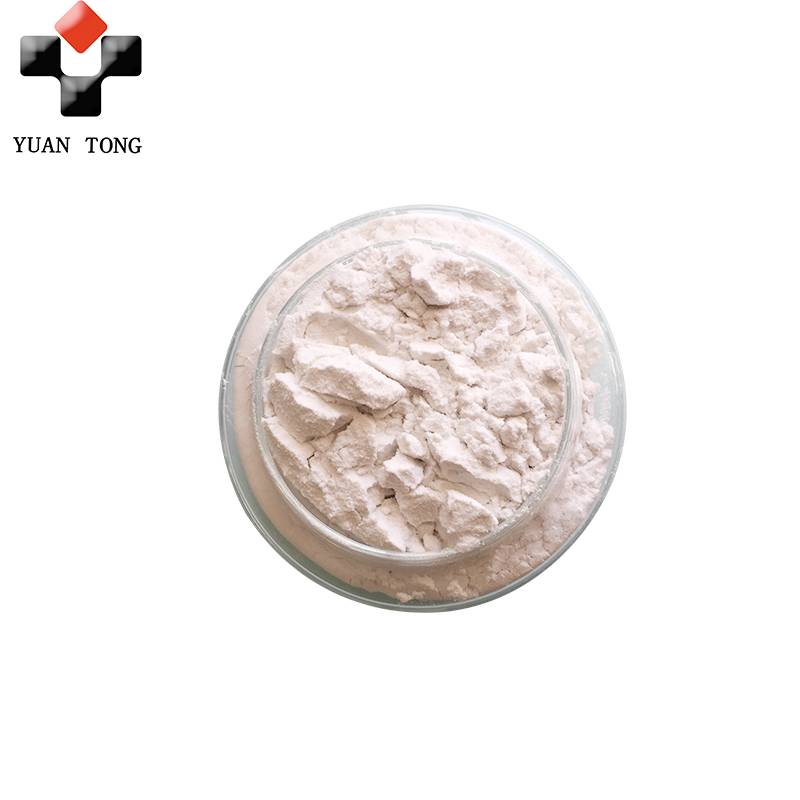
Filter Aid Diatomite For Fresh Water © 2023 · CBB Media LLC