We use cookies to enhance your experience. By continuing to browse this site you agree to our use of cookies. More info.
The aim of this article is to explain the principle of materialographic cutting as well as the consumables and parameters which can influence the cutting result. Cbn Tools
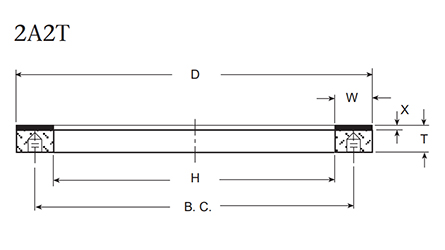
Metallographic cutting or sectioning usually marks the first step of the metallographic sample preparation process. In most cases it is necessary because the part or solid body is too large for the following metallographic grinding and polishing steps carried out on a laboratory scale. Depending on part geometries and material hardness as well as employed analytical techniques, different cutting techniques and consumables are used.
Amongst the mechanical sectioning processes, wet abrasive sectioning is the most frequently used technique for the materialographic analyses, because it has a lowest deformation during the cutting process. It is suitable for the thin sectioning of hard materials and applicable to almost all solids. The exceptions include very soft polymers or rubber materials, but even then, there is still application potential.
In general, in the abrasive sectioning a small plastic deformation zone is observed which is commonly below a depth of 200 µm from the cut surface. This means that the grinding and polishing steps can be drastically reduced because there is less material to remove to reach the true microstructure.
However, curved cuts or complex sample geometries are not possible with this approach; in these cases, a saw, mainly a wire or band saw, can be applied. For the thin cutting there is a technique named microtomy. This technique is standard in polymer industry and biology with limited applicability on hard and brittle materials since a defined blade is used for cutting.
Cutting very soft and ductile materials like very hard and brittle ones can be optimized by choosing the appropriate cutting discs. As a rule, the following principle applies: Soft-bonded wheels are suitable for cutting harder materials, whereas hard-bonded wheels for cutting soft materials.
To start the wet abrasive cutting process, the part is placed and fixed in the clamping device in the cut-off machine. The user must then select the appropriate consumables, set the correct parameters, and place the cut off wheel into position. Consequently, the user must initiate the automated or manual sectioning process. After the sample has been sectioned, it can be removed and cleaned and then it is ready for use.
The following requirements apply to sampling:
Two versions are possible in this case:
1. The sample table with the workpiece previously fixed on it is moved to the fixed cut-off wheel manually or automatically.
2. The cut-off wheel is moved accordingly.
The workpiece to be cut is firmly fixed on the cutting table. The cut-off wheel is then manually or automatically guided from top to bottom into the fixed workpiece.
The workpiece is not cut in one cutting step, but in layers (stepwise). This type of cut is particularly suitable for cutting the large, thick workpieces of solid material.
The workpiece is not cut in one cutting step, but in layers (stepwise). This type of cut is particularly suitable for cutting the large, thick workpieces of solid material that must be clamped on edge (plates, angles, etc.).
In case of a diagonal cut, the table moves backwards (X axis) and the cut-off wheel moves downwards (Y axis) at the same time. This type of cut is particularly suitable for cutting asymmetrical workpieces, or for compensating the wear of the cut-off wheel to obtain a constant cutting depth.
The workpiece is not cut in one cutting step, but in layers (stepwise). The zig-zag cut is made in the middle of the component.
During manual cutting, the clamping table (X axis) moves back and forth until the cut is completed. It starts with the movement from front to back. This type of cut is particularly suitable for workpieces where a clean cutting edge and material-friendly processing (temperature, deformation) is required due to the smallest possible contact surface.
This process is most often used on precision cut-off machines. It can also be used for large workpieces with corresponding rotary sample holders. The sample is turned clockwise or anti-clockwise towards the cut-off wheel. Quarter or half rotations are also possible. For a round workpiece with a diameter of 50 mm, only a cutting distance of 25 mm is required.
Wear (i.e., abrasion resistance), service life and cutting performance are decisive for the quality of the cut-off wheel. Abrasive agents (Aluminum oxide, Silicon carbide, Diamond, Cubic boron nitride (CBN), etc.) and bonding (metal, synthetic resin, or rubber) are characteristics of the wheel composition.
The available QATM abrasive materials are listed below:
The grain size of the abrasive in the cut-off wheel is an aspect that must not be neglected when cutting materialographic samples. It should be between 45 and 180 μm. This allows an optimally cut surface, which should facilitate further preparation, provided all parameters are observed. A very fine grain size is recommended when using thin cut-off wheels. A fine grain size is also important if burr-free cutting is required.
The degree of hardness of a wet abrasive cut-off wheel does not say anything about the hardness of the abrasive grains, but rather about the hardness of the bond, i. e. about the resistance of the individual abrasive grain to breaking out of the bond material.
Figure 1. QATM Al2O3 cut-off wheels with rubber (left side) and synthetic resin bond (right side) Image Credit: QATM
Optimum cooling is essential during cutting. Excessive heat development during the cutting process damages the specimen as well as the cut-off wheel. The purpose of anti-corrosion coolant is to protect the machine and specimen from corrosion and to improve stock removal by providing suitable lubrication during the cutting process. Commonly the appropriate pH value for this purpose is between 9 and 10. To improve the cooling performance QATM’s coolants have higher boiling points than water.
The most common anti-corrosion coolants are the aqueous solutions which have a medium cooling performance and reasonable capacity to carry the abrasive residuals.
Figure 2. QATM anti-corrosion coolants Image Credit: QATM
A vast range of different clamping tools and systems is available for all QATM cut-off machines. With our clamping tools, any sample size and material are safely fixed for accurate cutting procedures. Our clamping tools include:
Figure 3. QTool clamping tool which can be fixed directly on the working table. Image Credit: QATM
The main error that the user must avoid during wet abrasive cutting is excessive heat generation, due to insufficient cooling. In this case, the generated heat causes the materials microstructure to be unpredictably altered in an impermissible way – it no longer represents the original material structure. This happened with the sample shown in figure 43 on the left side. The intensive tarnish colors are unmistakable, compared to the correctly cut sample in the figure on the right.
Figure 4. Samples which were cut with inappropriate cutting parameters Image Credit: QATM
Further cutting artefacts can be found in our materialographic sampling guide titled Expert Guide Materialograpy/Metallography. The following link provides a reading sample and information on receiving the Expert Guide.
This article is an introduction to the principles of materialographic sampling (cutting). For more details, please refer to our guide to materialographic sampling titled Expert Guide, which can help you deepen your information on this topic.
This information has been sourced, reviewed and adapted from materials provided by QATM.
For more information on this source, please visit QATM.
Please use one of the following formats to cite this article in your essay, paper or report:
QATM. (2023, April 11). The Basics of Materialographic Sectioning. AZoM. Retrieved on November 30, 2023 from https://www.azom.com/article.aspx?ArticleID=21933.
QATM."The Basics of Materialographic Sectioning".AZoM.30 November 2023.
QATM. "The Basics of Materialographic Sectioning". AZoM. https://www.azom.com/article.aspx?ArticleID=21933. (accessed November 30, 2023).
QATM. 2023. The Basics of Materialographic Sectioning. AZoM, viewed 30 November 2023, https://www.azom.com/article.aspx?ArticleID=21933.
Do you have a question you'd like to ask regarding this article?
AZoM.com - An AZoNetwork Site

Diamond Grinding Stone Owned and operated by AZoNetwork, © 2000-2023