When considering upgrades, repairs, or new tube bending machines, metal fabrication shops should look beyond the equipment's technical capabilities and focus on business as a whole.
Contemplating buying a new CNC tube bender? Here are a few things to consider as you weigh factors like automation, repair, and replacement. Viga Atomization Equipment
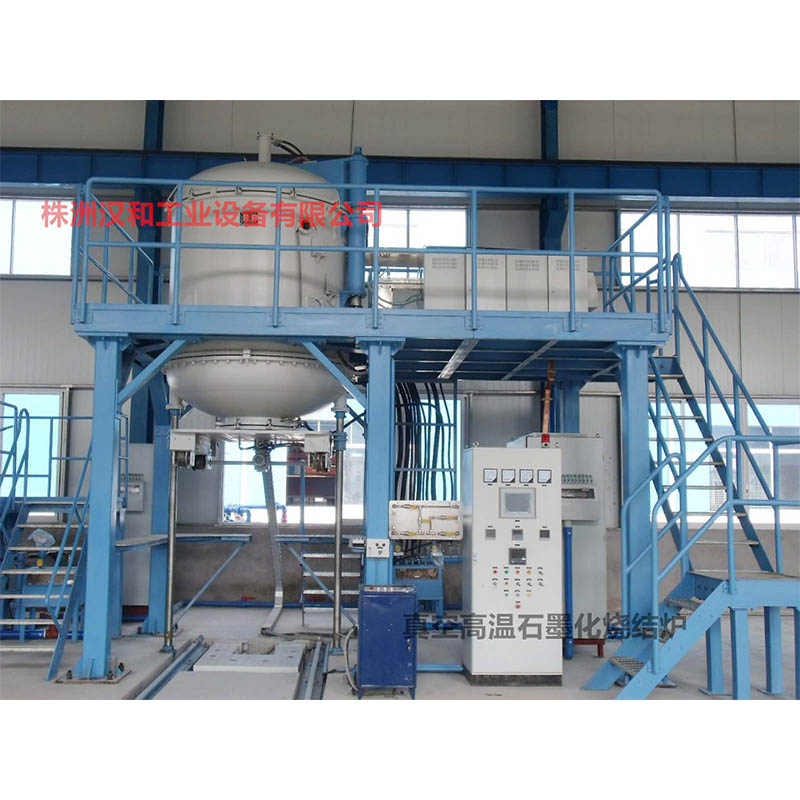
Almost every conversation I’ve had about new CNC tube benders has started with the size of the machine. However, after going through the process with several customers over the past couple of months, I realized how unique the decision-making process can be for each customer.
Most manufacturers specify the size of their machines based on the maximum outside diameter of the tubing. However, this does not necessarily paint a complete picture of the machine’s capability. Bed length, axis speeds, maximum and minimum bending radii, multistack, multiradius, and many other factors should weigh into your decision.
“When we are talking to our customers about new benders, one of the questions we ask is, ‘Can you open up new opportunities by embracing new or different technologies?’” said Mike Thomas, president of Tube Form Solutions. “Adding capabilities like push bending that will allow you to combine traditional rotary draw bending and roll bending for larger bend radii in the same machine set up may allow you to go after bending projects that you could not before.”
Here are some examples of options and benefits:
Other machine features that may help improve your capability or provide better cycle times include a swing-away wiper, independent bend die rotation, and carriage boost.
For high-volume production, automating bending processes can provide a rapid return on the additional investment. However, even lower-volume production can sometimes benefit from complete or even partial automation of the bending process, freeing an operator to focus on other tasks such as packaging or assembly.
“Even if you are not ready to build out a fully automated production cell right away, when considering a new tubing bender, give some weight to a machine whose mechanical design and control system will make it easier to automate in the future,” suggested Universal Tool and Engineering Owner Jamie Abraham.
If you are already bending tubing, you know that a new machine may be a huge initial investment—but the bigger value may be in the tooling you already own. Buying a new machine from a manufacturer that does not use the same tool mounts as your existing tooling may create a need for a larger investment than intended.
Specific machine capabilities may make it possible to adapt the machine to existing tools. Specifically, multistack capabilities can allow more flexibility in adding adapters to the project so you can use your existing tooling. A machine with servo capability for the vertical movement of the tube relative to the bend die provides maximum flexibility to use existing tools with the new machine.
The decision to repair or replace a tube bending machine must incorporate a broader spate of factors than machine size or capacity. You have to consider your entire business.
Buying a used or refurbished tube bender may make more sense than buying new.
If you are already forming tubes, finding an immediately available machine that works with your existing tooling won’t just increase your production capacity, it will provide redundancy when one of your production machines inevitably breaks down. Pre-owned machines can provide years of reliable service at a much lower initial cost—and often a better decision-to-delivery timeline.
We often work with customers who are struggling with the decision between repairing existing equipment or replacing it with new. Here are few benefits of new machines:
Finally, how you finance a machine can have a positive impact on the bottom line.
Borrowing may preserve cash for ongoing operations, or a lease may allow you to count every payment as an operating expense rather than just the interest. Work closely with your accountant and financial institution to come up with a finance plan that works for you.
See More by Jay Robinson
Read more from this issue
Subscribe to The Tube & Pipe Journal
The Tube & Pipe Journal became the first magazine dedicated to serving the metal tube and pipe industry in 1990. Today, it remains the only North American publication devoted to this industry, and it has become the most trusted source of information for tube and pipe professionals.
Easily access valuable industry resources now with full access to the digital edition of The Fabricator.
Easily access valuable industry resources now with full access to the digital edition of The Welder.
Easily access valuable industry resources now with full access to the digital edition of The Tube & Pipe Journal.
Easily access valuable industry resources now with full access to the digital edition of The Fabricator en Español.
Greg Davis of Red Beard's Garage joins hosts Josh Welton and Rafael Guerrero to talk about his wildly...
© 2023 FMA Communications, Inc. All rights reserved.
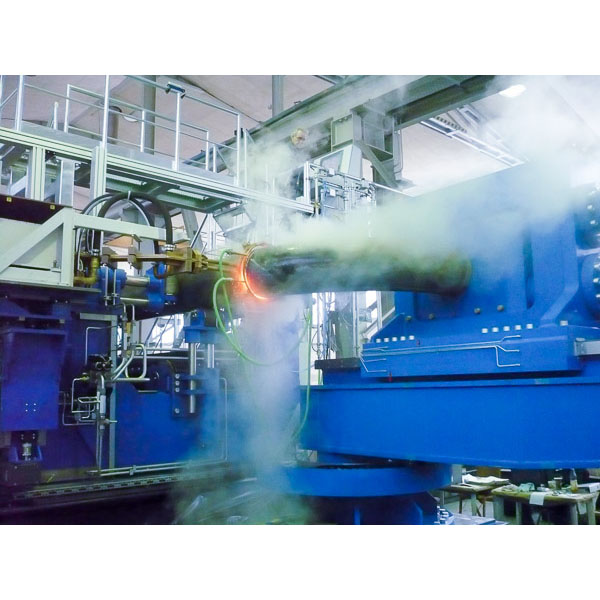
Induction Tube Bender Not yet registered? Sign up