Leaf springs, a holdover from the days of the horse and carriage, are a critical part of some heavy-duty vehicle suspension systems.
While function hasn’t changed, composition has. Today’s leaf springs are made from steel or metal composites that usually provide trouble-free performance, says Dave McCleave, director of aftermarket for Hendrickson. Because they’re not as prone to issues as other parts, they may often be overlooked during vehicle inspections. Trailer Suspension Fixed Torque Arm
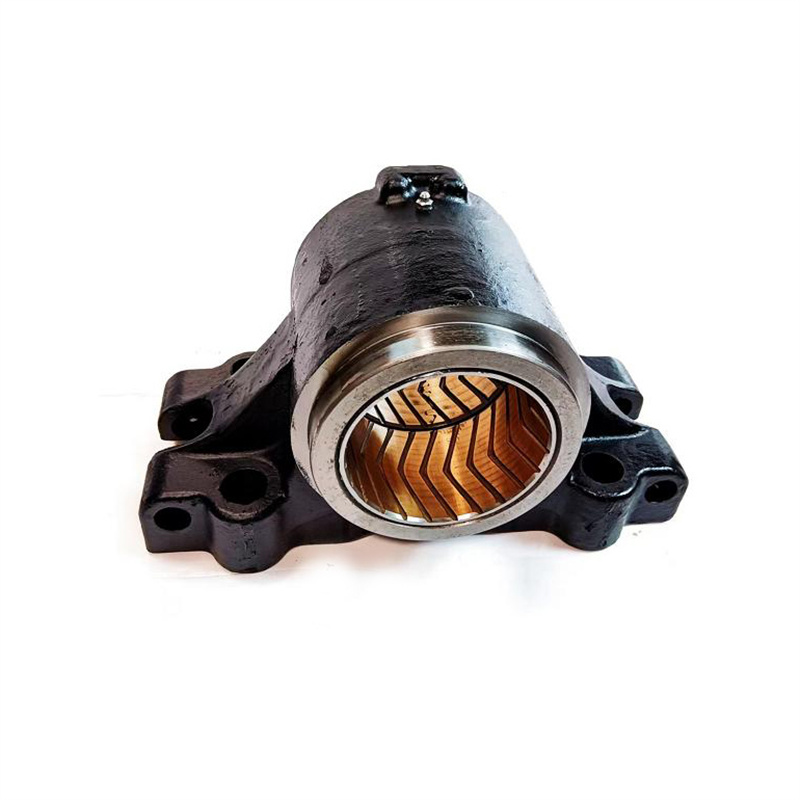
You may need to give your leaf springs a once-over if you notice your load sagging, says Reyco Granning junior project engineer Chris Gumbel. Other signs that it’s time to check your leaf springs include sagging without a load, trouble hauling, the suspension bottoming out, slouching to one side and diminished handling.
For steel leaf springs, McCleave says to check the individual leaves for any signs they are out of position. You should also look for cracks or fractures, excessive wear or fretting and for sagging or bent leaves.
[RELATED: Hendrickson releases lightweight suspensions for EV market]
McCleave says for leaning loads, you should measure from the frame rail to the ground on a level surface, and make sure to consult your technical bulletins for accurate measurements. In steel springs, the cracks are progressive, meaning they start out small and gradually become larger. Inspecting the springs as soon as you suspect a problem can catch problems when they’re still small.
Composite springs also crack and can display excessive wearing when it’s time for replacement, McCleave says, and can also fray. Some fraying is normal, he says, and you should consult your springs manufacturer to make sure any fraying you see is regular wear.
Also check for center bolts that are bent, loose or broken; U-bolts that are placed and torqued properly; and spring eyes and spring eye bushings that are damaged, distorted or worn.
Replacing problem springs during an inspection can save downtime and money rather than waiting until the part fails during operation, McCleave says.
Experts across the board say to go with OE-approved replacement springs.
“There are definitely bad spring makers out there,” Gumble says. “Aftermarket springs can be had for less money, however, they also may not live up to the original design intent.”
When replacing leaf springs, McCleave recommends vehicle owners replace worn springs with a quality product. Some things to look for:
You should also consider your capacity and ride height when choosing a new leaf spring, says John Devany, vice president of sales for Betts Truck Parts & Service.
You may need to give your leaf springs a once-over if you notice your load sagging,
While each replacement is different, broadly speaking, the process can be boiled down to a few steps, Devany says.
Gumble cautions while the replacement process seems simple, technicians would be well-served to pay heed to technical bulletins and specifications, particularly any pertaining to torque and tightening sequences. He adds the joint should be retorqued after 1,000-3,000 miles. Failure to do so, Gumble says, can result in loosening the joint and spring failure.
Leaf spring replacements are straightforward, experts say, but there are problems. Leaf springs are heavy and can be difficult to remove and install, resulting in unexpected parts being damaged or broken, including parts that are attached to the technician.
“Safe handling procedures such as using heavy lifting equipment, wearing gloves and eye protection are always recommended,” McCleave says.
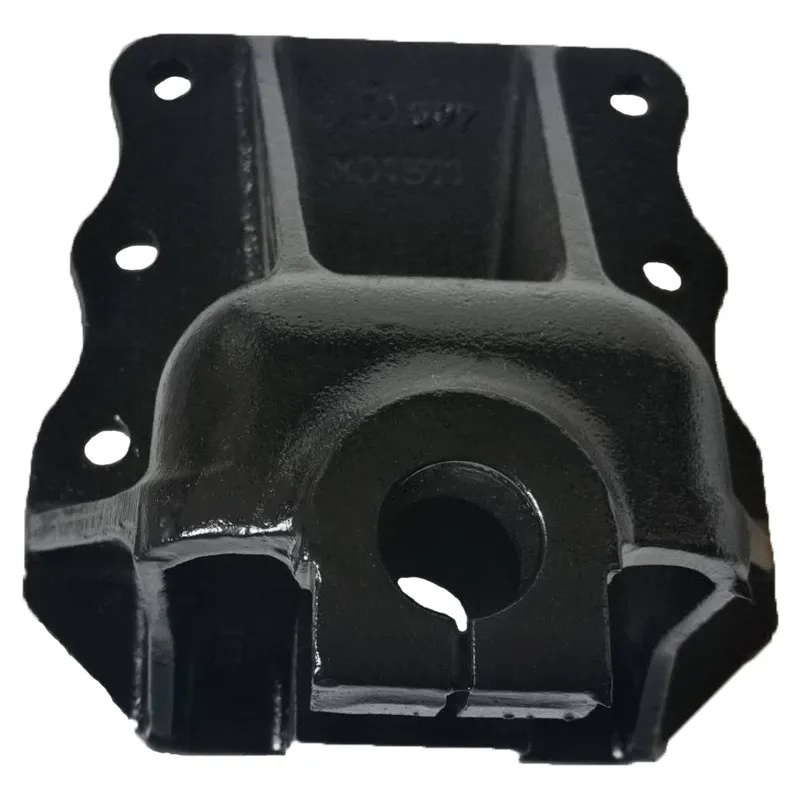
Mitsubishi Truck Spring Bracket Pins and bolts can also be rusted or damaged and have to be cut off; again, experts recommend technicians wear proper personal protective gear and use the right tool for the job.